Keywords
Computer Science and Digital Science
- A5.5.1. Geometrical modeling
- A5.5.2. Rendering
- A8.3. Geometry, Topology
Other Research Topics and Application Domains
- B5.7. 3D printing
1 Team members, visitors, external collaborators
Research Scientists
- Sylvain Lefebvre [Team leader, INRIA, Senior Researcher, HDR]
- Xavier Chermain [INRIA, Researcher]
- Jonas Martinez Bayona [INRIA, Researcher]
- Camille Schreck [INRIA, Researcher]
Faculty Member
- Cedric Zanni [Université de Lorraine, Associate Professor]
Post-Doctoral Fellow
- David Jourdan [INRIA]
PhD Students
- Eduardo Aguilar Segovia [INRIA, from Oct 2022]
- Melike Aydinlilar [Université de Lorraine]
- Semyon Efremov [INRIA, until May 2022]
- Jimmy Etienne [Université de Lorraine, ATER]
- Marco Freire [Université de Lorraine]
- Thibault Tricard [Université de Lorraine, until Apr 2022]
Technical Staff
- Pierre-Alexandre Hugron [INRIA, Engineer]
- Salim Perchy [INRIA, Engineer, until Sep 2022]
- Nathaniel Seyler [Université de Lorraine, Engineer]
Interns and Apprentices
- Simon Hergott [INRIA, from Apr 2022 until Apr 2022]
- Florian Mathieu [INRIA, Intern, from Apr 2022 until Jul 2022]
Administrative Assistants
- Hélène Cavallini [INRIA, from Sep 2022]
- Véronique Constant [INRIA]
2 Overall objectives
Digital fabrication has had a profound impact on most industries. It allows complex products to be modeled in Computer Assisted Design (CAD) software and then sent to Computer-Aided Manufacturing (CAM) devices that physically produce the products. Typical CAM devices are computer-controlled lathes and milling machines that are ubiquitous in mass-production chains, along with injection molding and assembly robots. The design of a new product requires a large pool of expertise consisting of highly skilled engineers and technicians at all stages: design, CAD modeling, fabrication, and assembly chains.
Within CAM technologies, the advent of Additive Manufacturing (AM) (i.e., 3D printing) together with powerful and inexpensive computational resources let us envision a different scenario. In particular, these technologies excel where traditional approaches find their limitations:
- Parts with complex geometry can be fabricated in a single production run, and in most situations the cost is not significantly impacted by the geometric complexity.
- The cost-per-unit for fabricating an object is constant and significantly lower than producing a small series of objects with traditional means. Though it is not competitive on a mass-production scale where the cost-per-unit decreases as the number of produced units increases.
- The machine setup is largely independent of the object being fabricated, and thus these technologies can be made available through generic 3D printing companies and online print services. Additionally, the machines are significantly easier to operate than traditional fabrication means. This makes them accessible to the general public, and well suited for rapid design iterations and prototyping.
Consequently, it becomes possible to design and produce parts with short development cycles: physical objects are uniquely and efficiently fabricated from digital models. Each object can be personalized for a specific use or customer. The core difficulty in this context lies in modeling parts, and this remains a significant obstacle as functional, and manufacturability constraints have to be enforced. By functional constraint, we refer here to some desired behavior in terms of rigidity, weight, balance, porosity, or other physical properties. This is especially important as AM allows the fabrication of extremely complex shapes, the scales of which vary from a few microns to a few meters. All this pushes AM well beyond traditional means of production and enables the concept of metamaterials; materials where parameterized microstructures change the behavior of a base shape fabricated from a single material.
Exploiting this capability turns the modeling difficulties into acute challenges. Such a quantity of details modeling becomes intractable, and specifying the geometry with standard tools becomes a daunting task, even for experts. Besides, these details have to interact in subtle and specific ways to achieve the final functionality (e.g., flexibility, porosity) while enforcing fabrication constraints. On the process planning side (i.e., the set of computations turning the part into printing instructions), large parts filled with microstructures, porosities, and intricate multi-scale details quickly lead to huge data-sets and numerical issues.
Our overall objective is to develop novel approaches enabling experts and practitioners alike to exploit the advantages of AM fully. We aim to achieve this by developing novel algorithms that automatically synthesize or complete designs with functional details. We consider the full chain, from modeling to geometry processing, to optimize 3D printer instructions.
3 Research program
We focus on the computational aspects of shape modeling and processing for digital fabrication: dealing with shape complexity, revisiting design and customization of existing parts in view of the novel possibilities afforded by AM, and providing a stronger integration between modeling and the capabilities of the target processes.
We tackle the following challenges:
- develop novel shape synthesis and shape completion algorithms that can help users model shapes with features in the scale of microns to meters while following functional, structural, geometric, and fabrication requirements;
- propose methodologies to help expert designers describe shapes and designs that can later be customized and adapted to different use cases;
- develop novel algorithms to adapt and prepare complex designs for fabrication in a given technology, including the possibility to modify aspects of the design while preserving its functionality;
- develop novel techniques to unlock the full potential of fabrication processes, improving their versatility in terms of feasible shapes as well as their capabilities in terms of accuracy and quality of deposition;
- develop novel shape representations, data-structures, visualization, and interaction techniques to support the integration of our approaches into a single, unified software framework that covers the full chain from modeling to printing instructions;
- integrate novel capabilities enabled by advances in additive manufacturing processes and materials in the modeling and processing chains, in particular regarding the use of functional materials (e.g. piezoelectric, conductive, shrinkable).
Our approach is to cast a holistic view on the challenges above by considering modeling and fabrication as a single, unified process. Thus, the modeling techniques we seek to develop will take into account the geometric constraints imposed by the manufacturing processes (minimal thickness, overhang angles, trapped material) and the desired object functionality (rigidity, porosity). To allow for the modeling of complex shapes and adapt the same initial design to different technologies, we propose developing techniques that can automatically synthesize functional details within parts. At the same time, we will explore ways to increase the versatility of the manufacturing processes through algorithms that are capable of exploiting additional degrees of freedom, can introduce new capabilities and improve part accuracy.
Our research program is organized along with three main research directions. The first one focuses on the automatic synthesis of shapes with intricate multi-scale geometries that conform to additive manufacturing technologies' constraints. The second direction considers geometric and algorithmic techniques for the actual fabrication of the modeled object. We aim to improve further the capabilities of the manufacturing processes with novel deposition strategies. The third direction focuses on computational design algorithms to help model parts with a gradient of properties and help customize existing designs for their reuse.
These three research directions interact strongly and cross-pollinate: e.g., novel possibilities in manufacturing unlock novel possibilities in terms of shapes that can be synthesized. Stronger synthesis methods allow for further customization.
4 Application domains
4.1 Digital Manufacturing
Our work addresses generic challenges related to fabrication and can thus be applied in a wide variety of contexts. Our aim is first and foremost to develop the algorithms that will allow variously industrial sectors to benefit more strongly from the potential of AM. To enable this, we seek collaborations with crucial industry partners developing software and AM systems for a variety of processes and materials that are of interest to specific sectors (e.g., dental, prosthetic, automotive, aerospace).
4.2 Medical Applications
To allow for faster transfer of our techniques and unlock novel applications, we actively seek to develop applications in the medical sector. In particular, we are involved in a project around the design of orthoses, which explores how our research on elasticity control through microstructure geometries can be specifically applied to the medical sector.
5 Highlights of the year
In 2022 we presented new results on support generation for 3D printing, improving on a prior method with a faster approach that – remarkably – avoids connecting the support structure to the part if such a solution exists 10.
We proposed a novel approach to generate infill trajectories that are both cyclic and can be oriented according to a control field 7. This method is the first to achieve such a result.
We obtained new results on the efficient rendering of implicit surfaces 9 as well as curved 3D printing 8.
We continued exploring these topics throughout the year, with several advances being submitted to 2023 venues.
5.1 Awards
Jonàs Martínez was nominated Young Research Fellow (Eurographics French Chapter): an honorary title awarded annually by a jury to a young researcher established in a French institution in recognition of his scientific excellence in computer graphics.
6 New software and platforms
6.1 New software
6.1.1 IceSL
-
Keyword:
Additive manufacturing
-
Scientific Description:
IceSL is the software developed within MFX, that serves as a research platform, a showcase of our research results, a test bed for comparisons and a vector of collaborations with both academic and industry partners. The software is freely available both as a desktop (Windows/Linux) and as an online version.
-
Functional Description:
IceSL allows users to model complex shapes through CSG boolean operations. Objects can be directly prepared and sent to a 3D printer for fabrication, without the need to compute an intermediate 3D mesh.
-
News of the Year:
In the past year IceSL saw a number of new features added. The plugin system was released to the public and is now officially supported by the team. Efforts on this include full-fledged examples of each type of plugin and detailed documentation of the interfaces as well as the examples themselves.
Our resin-based 3D printing module was also officially released and is now supported along with the other 3d printing modes in IceSL. This new module is also available in the web version, and it includes a novel support calculation method that was published by the team this same year.
Additionally, the user base of IceSL has been incrementing significantly w.r.t. the desktop version vis-à-vis an increase of more than 20K downloads (a 14% increase of cumulative downloads). The web version is now seeing upwards of one hundred uses per day (actual processing of a 3d model).
- URL:
-
Authors:
Sylvain Lefebvre, Frédéric Claux, Jonas Martinez Bayona, Jean Hergel, Jérémie Dumas, Samuel Hornus, Yamil Salim Perchy Bocanegra, Cedric Zanni, Pierre Bedell, Jimmy Etienne, Haichuan Song, Thibault Tricard, Pierre-Alexandre Hugron
-
Contact:
Sylvain Lefebvre
6.1.2 Silice
-
Name:
Silice
-
Keywords:
FPGA, Programming
-
Functional Description:
Silice makes it possible to write algorithms for FPGAs in the same way we write them for processors: defining sequences of operations, subroutines that can be called, and using control flow statements such as while and break. At the same time, Silice lets you fully exploit the parallelism and niceties of FPGA architectures, describing operations and algorithms that run in parallel and are always active, as well as pipelines. Silice remains close to the hardware: nothing gets obfuscated away. When writing an algorithm you are in control of what happens at which clock cycle, with predictable rules for flow control. Clock domains are exposed. In fact, Silice compiles to and inter-operates with Verilog: you can directly instantiate and bind with existing modules.
-
Release Contributions:
2021 version.
-
News of the Year:
Silice has been extended with an improved syntax to clarify bindings, support temporary expression declarations and improved register culling optimization.
Most importantly, it now features an advanced pipeline description functionality, enabling users to combine pipelines and algorithms (FSMs) with ease. Silice was presented by Sylvain Lefebvre at a tutorial session at the FCCM conference in 2022.
- URL:
-
Author:
Sylvain Lefebvre
-
Contact:
Sylvain Lefebvre
6.2 New platforms
Participants: Pierre Bedell, Pierre-Alexandre Hugron.
We continued our active participation within the Creativ'Lab, a common experimental platform funded by Inria, Loria, CNRS and Région Grand Est.
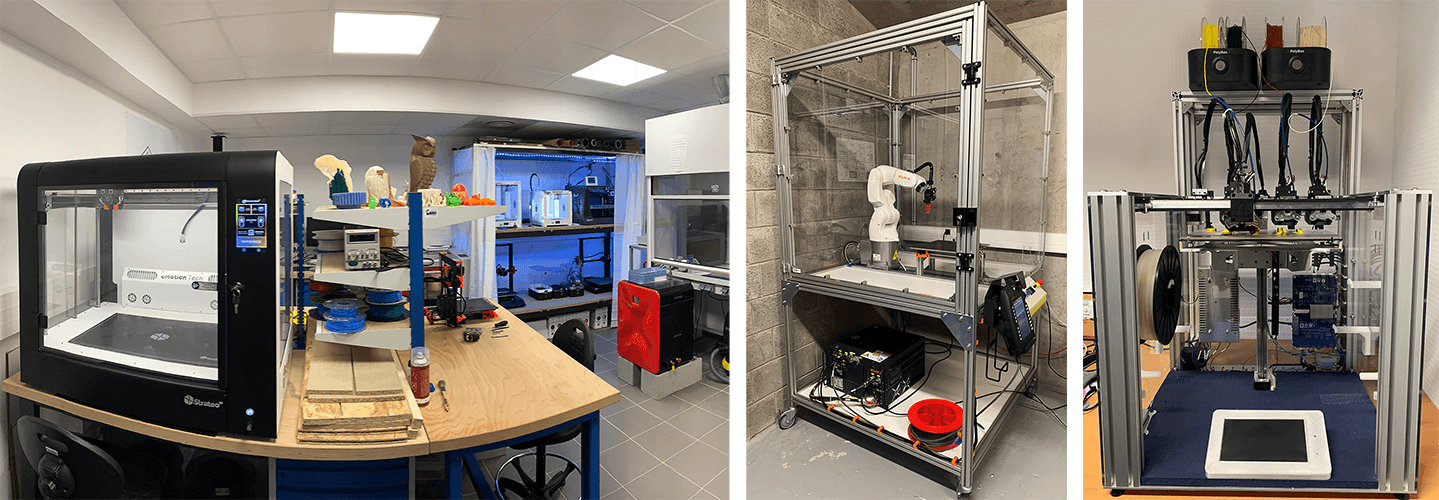
photography of the MFX experimenting room within the Creativ'lab
A second room was setup for resin printers and our 3D printing robot equipment, used in the context of our research on curved 3D printing. We acquired and installed a new FormLabs Form 3L printer. This room was completed by the addition of a fume extractor to avoid chemical exposure during manipulation. The room also hosts 3D printers of the LARSEN team, creating a collaborative space around resin printing and between both teams in general.
Our 3D printing robot arm (see figure 1, middle) is now installed in a cage with all safety equipment and it is ready to use for experiment.
A new 3D printer (E3D Toolchanger, see figure 1, right) with multi-material capability was setup. This machine is capable of extruding four different materials in the same part. It is targeted to print flexible material in the context of the DORNELL project. We also created a slicer profile to use this machine directly with IceSL.
As additional safety measures we installed additional air purifiers in our experimental rooms.
7 New results
7.1 Procedural bridges-and-pillars support generation
Participants: Marco Freire, Samuel Hornus, Salim Perchy, Sylvain Lefebvre.
Additive manufacturing requires support structures to fabricate parts with overhangs. In this paper, we revisit a known support structure based on bridges-and-pillars (see Figure 2). The support structures are made of vertical pillars supporting horizontal bridges. Their scaffolding structure makes them stable and reliable to print. We propose a novel algorithm for this type of supports, focusing on avoiding unnecessary contacts with the part as much as possible. Our approach builds upon example-based model synthesis to enable early detection of collision-free passages as well as non-reachable regions.
This work was presented by Marco Freire at Eurographics 2022 (short paper track 10).
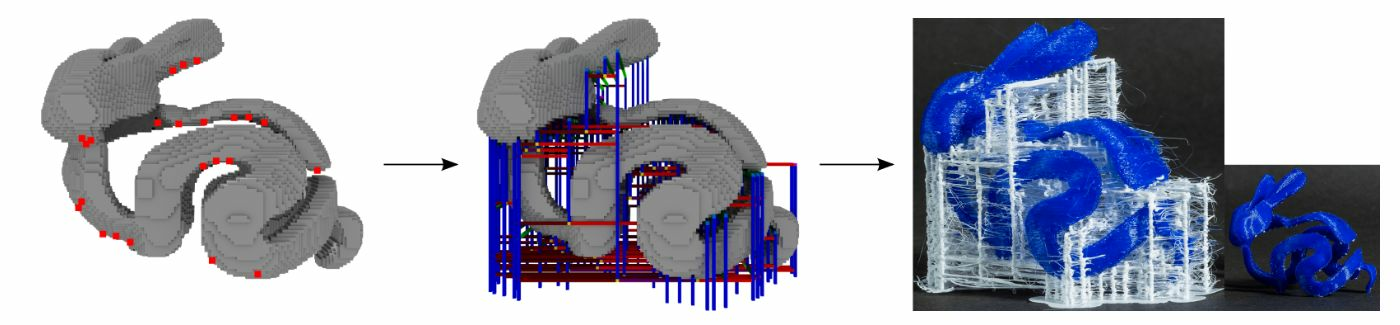
Showcase of the support generation process, virtual and printed result.
7.2 Closed space-filling curves with controlled orientation for 3D printing
Participants: Adrien Bedel, Yoann Coudert-Osmont, Jonàs Martínez, Rahnuma Islam Nishat, Sue Whitesides, Sylvain Lefebvre.
We explore the optimization of closed space-filling curves under orientation objectives. By solidifying material along the closed curve, solid layers of 3D prints can be manufactured in a single continuous extrusion motion. The control over orientation enables the deposition to align with specific directions in different areas, or to produce a locally uniform distribution of orientations, patterning the solidified volume in a precisely controlled manner.
This work was published at EUROGRAPHICS 2022 7 and presented by Yoann Coudert-Osmont. It received the reproducibility stamp and is available on github.
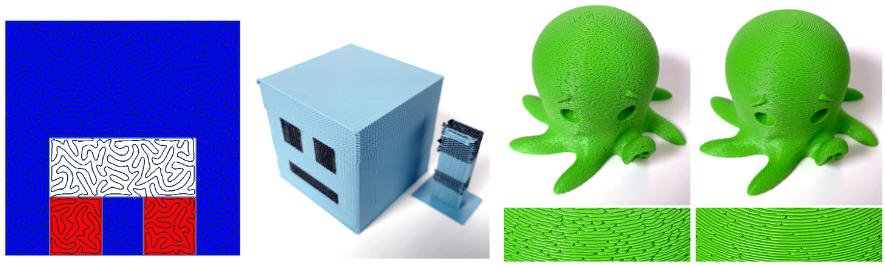
Optimization of cyclic deposition trajectories.
7.3 Transparent rendering and slicing of integral surfaces using per-primitive interval arithmetic
Participants: Melike Aydinlilar, Nathaniel Seyler, Cédric Zanni.
Scale-invariant integral surfaces, which are implicit representations of surfaces, provide a way to define smooth surfaces from skeletons with prescribed radii defined at their vertices. They can be used to represent a large range of shapes, from procedural foam structures to truss structures and artistic shapes (see Figure 4).
Transparent rendering and slicing of implicit surfaces can be done relying on the same base algorithm. We propose a novel algorithm based on tight field value interval ranges, derived from the integral field definition. When high precision is required, the method performs better than state of the art methods.
This work has been presented at the Eurographics 2022 (short paper track 9). The Computer Graphic Forum journal paper 14 has been presented at the same conference.
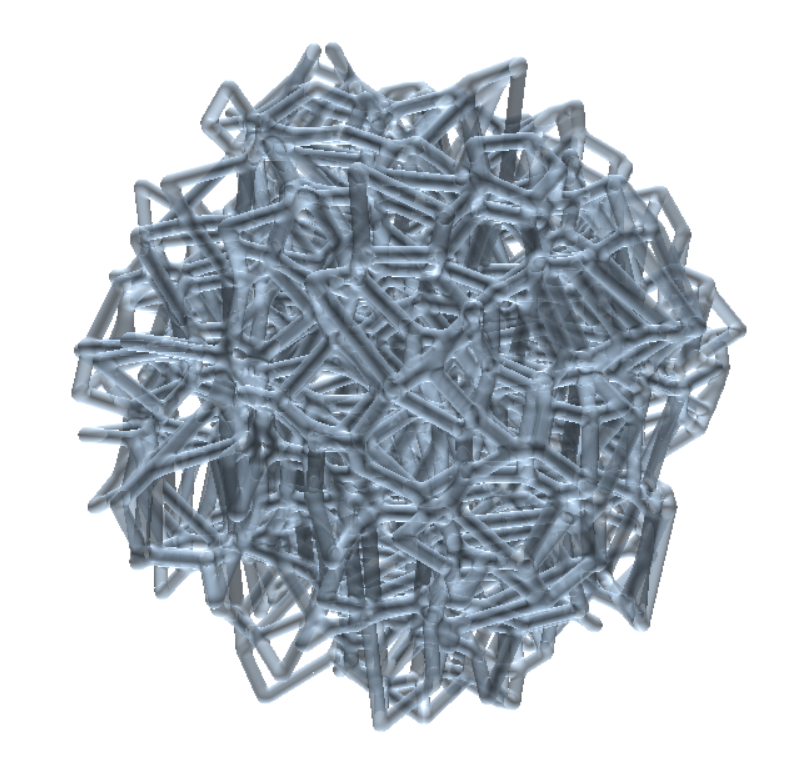
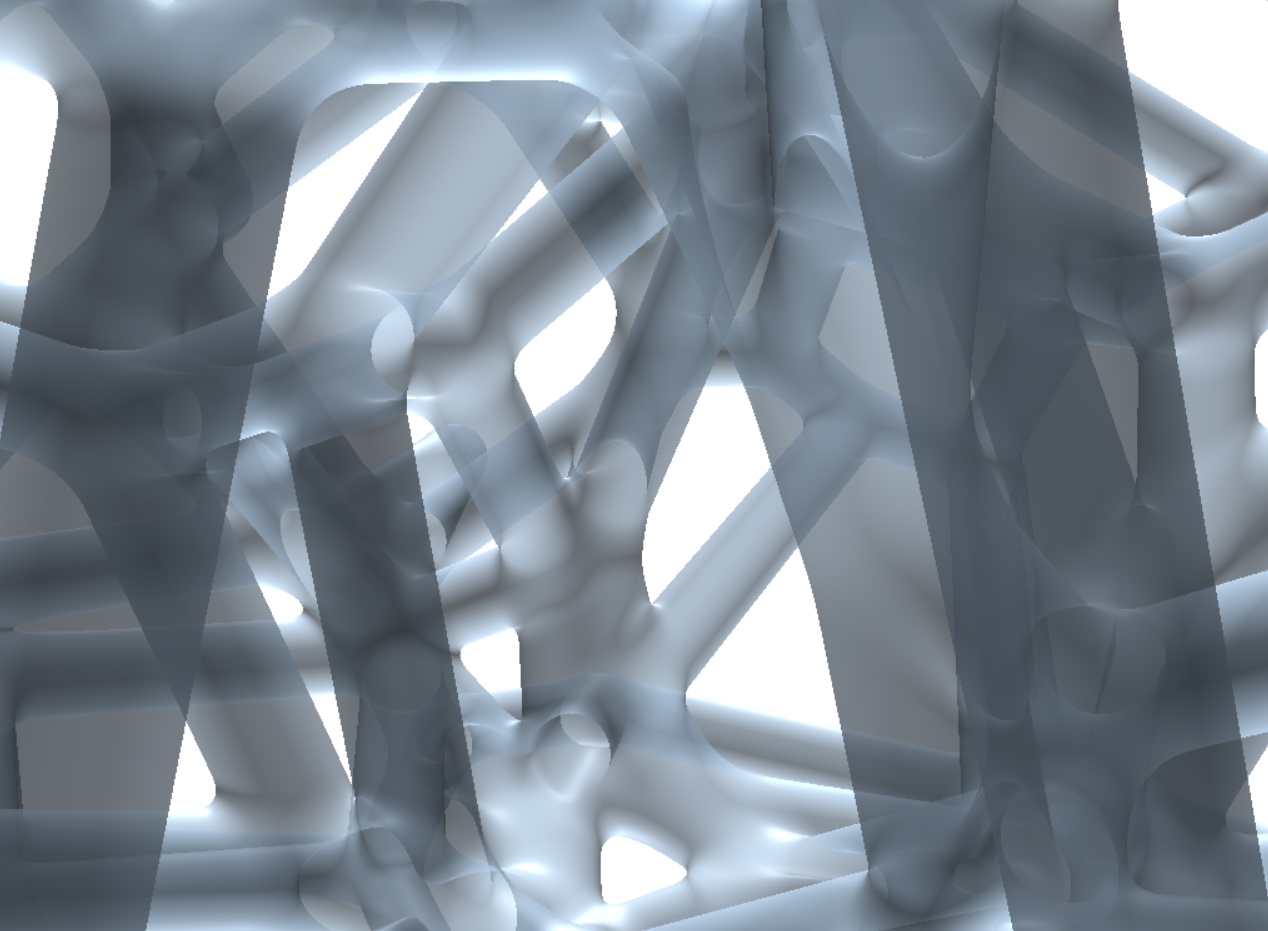
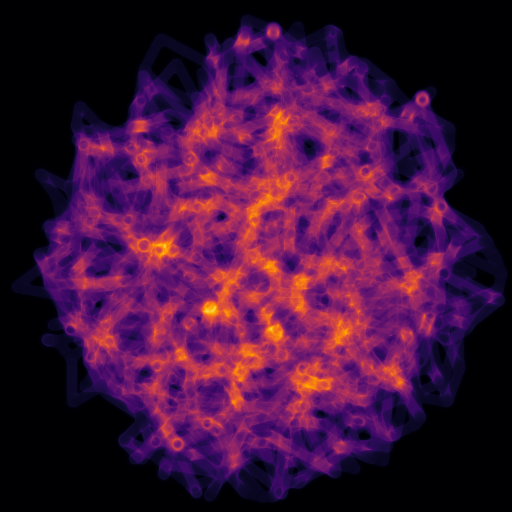
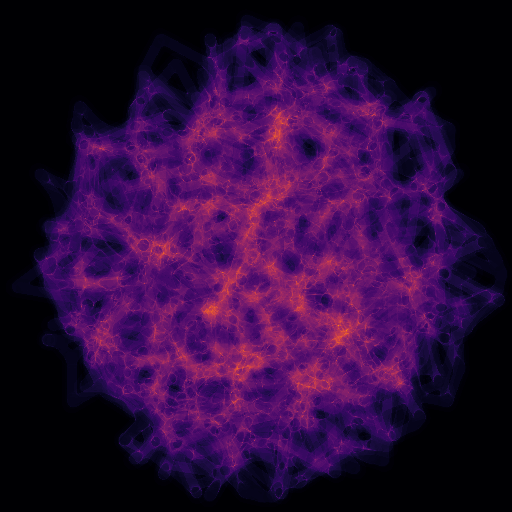
7.4 Curved 3D printing
Participants: Sylvain Lefebvre, Pierre-Alexandre Hugron, Salim Perchy, Jimmy Etienne.
We continued exploring the topic of curved 3D printing throughout 2022.
Sylvain Lefebvre joined a collaboration with colleagues of the University of Manchester, resulting in a publication at SIGGRAPH Asia 2022 8.
We are currently integrating curved printing into our software, IceSL, as illustrated in Figure 5.
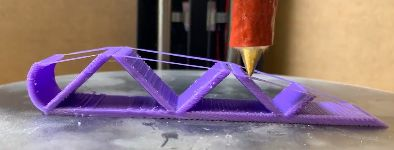
8 Bilateral contracts and grants with industry
8.1 Bilateral contracts with industry
Partnership with AddUp
- Company: AddUp.
- Duration: Started in 2019.
- Participants: Sylvain Lefebvre.
- Abstract: AddUp is a French manufacturer of metal 3D printers for high-end industrial applications. We announced during FormNext 2019 (November) a partnership towards the creation of new software technologies. This partnership continued to develop in 2022.
9 Partnerships and cooperations
9.1 National initiatives
9.1.1 ANR
ANR JCJC MuFFin
- Acronym: MuFFin.
- Title: Procedural Stochastic Microstructures for Functional Fabrication.
- Duration: 2018-2022.
- Coordinator: Jonàs Martínez.
- Participants: Jonàs Martínez, Sylvain Lefebvre, Samuel Hornus, Semyon Efremov.
-
Abstract:
MuFFin aimed at contributing a unified pipeline for the efficient and scalable synthesis, visualization, and modeling of additively manufactured microstructures with tailored macroscopic physical behavior. The project ended in June 2022.
ANR JCJC IMPRIMA
- Acronym: IMPRIMA.
- Title: Implicit modeling for additive manufacturing.
- Duration: 2019-2023.
- Coordinator: Cédric Zanni.
- Participants: Cédric Zanni, Sylvain Lefebvre, Melike Aydinlilar, Nathaniel Seyler.
-
Abstract:
Project IMPRIMA seeks to explore novel implicit representations to provide a unified approach for the modeling and slicing of both macro geometry, microstructures, and gradient of material. Additionally, this research aims to complete tight integration of both standard boundary representations and novel implicit volume representations, allowing the best choice of representation for different parts of a design.
Our latest results on the visualization of scale-invariant integral surfaces (SCALIS), a surface representation suited for the description of both micro and macro geometry, has lead to a short paper publication on transparent rendering and slicing 9 as well as two presentations to Eurographics 2022.
9.1.2 Inria
Inria Exploratory Action CONTINUA
- Acronym: AEx CONTINUA.
- Title: Continuous deposition of paste-like materials.
- Duration: 2022-2026.
- Coordinator: Jonàs Martínez.
- Participants: Jonàs Martínez, Luis Mollericon Titirico.
- Abstract: Additive Manufacturing (AM) with paste-like materials (e.g., clay, silicon) facilitates the production of large-scale structures, but it is particularly challenging for complex geometries. At the manufacturing stage, there is a high risk that the structure collapses under gravity, and defects appear due to repeated interruptions of the extrusion flow. In view of these challenges, prior work considers simple structures that do not take advantage of AM's full capabilities. CONTINUA will strive to study the space of manufacturable deposition paths to, ultimately, enable the AM of large-scale complex structures.
Inria Challenge DORNELL
- Acronym: DORNELL
- Title: A multimodal, shapeable haptic handle for mobility assistance of people with disabilities.
- Duration: 2022-2026.
- Coordinator: Marie Babel.
- Partners: Inria MFX, POTIOC,
- Participants (MFX): Camille Schreck, Pierre-Alexandre Hugron, David Jourdan, Sylvain Lefebvre.
- Abstract: While technology helps people to compensate for a broad set of mobility impairments, visual perception and/or cognitive deficiencies still significantly affect their ability to move safely and easily. DORNELL proposes an innovative multisensory, multimodal, smart haptic handle that can be easily plugged onto a wide range of mobility aids. Specifically fabricated to fit the needs of a person, it provides a wide set of tactile sensations in a portable and plug-and-play format – bringing haptics in assistive technologies all at once.
10 Dissemination
10.1 Promoting scientific activities
10.1.1 Scientific events: organisation
General chair, scientific chair
Jonàs Martínez was a co-chair of the Journées Françaises d'Informatique Graphique (jFIG 2022).
10.1.2 Scientific events: selection
Member of the conference program committees
Jonàs Martínez was part of the program committee of the Symposium on Solid and Physical Modeling (2022), the IEEE/RSJ International Conference on Intelligent Robots and Systems (2022), and the SIGGRAPH Asia Technical Communications and Posters (2022).
Camille Schreck was part of the program committee of Shape Modeling International 2022, Pacific Graphics 2022, SIGGRAPH Asia Technical Communications and Posters program, and the Journées Françaises d'Informatique Graphique (jFIG 2022).
Xavier Chermain was part of the program committee of Journées Françaises d'Informatique Graphique (jFIG 2022).
Cédric Zanni was part of the program committee of Journées Françaises d'Informatique Graphique (jFIG 2022).
Sylvain Lefebvre served on the advisory board of the IPC of EUROGRAPHICS 2023.
Reviewer
Jonàs Martínez was a reviewer for SIGGRAPH 2022 and SIGGRAPH Asia 2022.
Camille Schreck was a reviewer for SIGGRAPH 2022 and SIGGRAPH Asia 2022.
Sylvain Lefebvre was a reviewer for SIGGRAPH 2022.
10.1.3 Journal
Jonàs Martínez was a reviewer for the journals Computer Graphics Forum and IEEE Transactions on Visualization and Computer Graphics.
Camille Schreck was a reviewer for the journal Computer-Aided Design (CAD).
10.1.4 Invited talks
David Jourdan was an invited speaker at the University Liverpool (11/12 keynote).
Sylvain Lefebvre gave an invited talk at the Graphyz2 conference (Graphyz2) together with Corentin Coulais (TU-Delft).
Sylvain Lefebvre was invited to present Silice during a tutorial at the IEEE Symposium on Field-Programmable Custom Computing Machines in June 2022.
Thibaut Tricard and Sylvain Lefebvre gave invited presentations in the Computational Fabrication web series (link).
10.1.5 Scientific expertise
Sylvain Lefebvre served as an expert on an HCERES committee.
10.1.6 Research administration
Sylvain Lefebvre is the head of the Commission du Développement Technologique (CDT) of the Inria Nancy Grand-Est center.
10.2 Teaching - Supervision - Juries
10.2.1 Teaching
- Master: Jonàs Martínez, Introduction to data parallelism, 30h ETD, Université de Lorraine, France.
- Master: Jonàs Martínez, Advanced machine architectures (GPU), 32h ETD, Télécom Nancy, France.
- Master: Cédric Zanni, Software Engineering, 31.5h ETD, M1, École des Mines de Nancy, France.
- Master: Cédric Zanni, Introduction to C/C++, 27h ETD, M1, École des Mines de Nancy, France.
- Master: Cédric Zanni, Techniques for video game programming, 27h ETD, M1, École des Mines de Nancy, France.
- Master: Cédric Zanni, ARTEM Game Lab, 22h ETD, M1, École des Mines de Nancy, France.
- Master: Cédric Zanni, Outils informatique, 12h ETD, L3, École des Mines de Nancy, France.
- Master: Sylvain Lefebvre, Additive manufacturing for soft robotics, 6h ETD, École Polytechnique, Saclay, France.
- Master: Sylvain Lefebvre, Algorithms for additive manufacturing, 12h ETD, Master M2 AVR, Nancy, France.
- Master: Sylvain Lefebvre, Introduction to additive manufacturing, 6h ETD, ENSEM Nancy, France.
- Master: Sylvain Lefebvre, Hardware design on FPGA, 12h ETD, Telecom Nancy, France.
- Master: Thibault Tricard, ARTEM Game Lab, 24h ETD, M1, École des Mines de Nancy, France.
- Master: Thibault Tricard, Introduction to data parallelism, 12h ETD, Université de Lorraine, France.
- Master: Camille Schreck, Introduction to 3D Graphics, 26h ETD, Telecom Nancy, France.
- Master: Camille Schreck, Introduction to additive manufacturing, 6h ETD, ENSEM Nancy, France.
- Master: Camille Schreck, 3D Graphics and Parallelism, 12h ETD, ENSG Nancy, France.
- License : Cédric Zanni, Introduction to Computer Science, 14h ETD, L3, École des Mines de Nancy, France.
- License: Marco Freire, Software development and programming methodology, 10h ETD, Université de Lorraine, France
- License LP AFTER: Sylvain Lefebvre, 3D printing with IceSL, 6h ETD, Université de Lorraine, France
- License FACDR: Sylvain Lefebvre, 3D printing with IceSL, 6h ETD, Université de Lorraine, France
- License: Marco Freire, Digital culture and tools, 14h ETD, Université de Lorraine, France
- License: Marco Freire, Algorithms and programming 2, 40h ETD, Université de Lorraine, France
- BUT: Jimmy Etienne, Introduction to programming, 56h ETD, IUT Charlemagne (Nancy), France.
- BUT: Jimmy Etienne, Second year project supervision, 8h, IUT Charlemagne (Nancy), France.
10.2.2 Supervision
- Defended PhD : Jimmy Etienne, Curved slicing for additive manufacturing 12, started in 2018, advisors: Sylvain Lefebvre, Cédric Zanni.
- Defended PhD : Thibaut Tricard, Procedural noises for the design of small-scale structures in Additive Manufacturing 13, started in 2018, advisors: Sylvain Lefebvre, Didier Rouxel.
- Defended PhD : Semyon Efremov, 3D periodic cellular materials with tailored symmetry and implicit grading 11, started in 2013, advisors: Jonàs Martínez, Sylvain Lefebvre.
- PhD in progress : Melike Aydinlilar, Implicit modeling for additive manufacturing, started November 2019, advisors: Cédric Zanni, Sylvain Lefebvre.
- PhD in progress : Marco Freire, Layout problems in Computer Graphics and beyond, started in 2020, advisor: Sylvain Lefebvre.
- Internship: Continuous Paths Deposition, 12 weeks, Florian Mathieu, L3, Université de Lorraine, France, advisors: Pierre-Alexandre Hugron, Sylvain Lefebvre.
- Internship: Thorough Testing of DLP Support Methods, 3 weeks, Simon Hergott, L1, Université de Lorraine, France, advisors: Pierre-Alexandre Hugron, Sylvain Lefebvre.
10.2.3 Juries
Jonàs Martínez was a reviewer for the PhD thesis of Tim Felle Olsen (Technical University of Denmark).
Sylvain Lefebvre was a reviewer on the doctoral committee of Tim Kuipers (TU Delft / Ultimaker) and Elie Michel (Telecom Paris), an examiner of the doctoral committee of Pascal Guehl (Strasbourg University) and Félix Vanneste (Université de Lille), and an external expert on the doctoral committee of Emmanuel Rodriguez (Grenoble University).
10.3 Popularization
10.3.1 Interventions
Sylvain Lefebvre gave an invited presentation to students from ENS Lyon during their sport-etude week.
We have organized three different IceSL Workshops, to teach how to use IceSL to our partners from the DORNELL project.
11 Scientific production
11.1 Major publications
- 1 articleFast ray tracing of scale-invariant integral surfaces.Computer Graphics Forum406September 2021, 117-134
- 2 articleBridging the Gap: Automated Steady Scaffoldings for 3D Printing.ACM Transactions on Graphics334July 2014, 98:1 - 98:10
- 3 articleCurviSlicer: Slightly curved slicing for 3-axis printers.ACM Transactions on Graphics384August 2019, 1–11
- 4 articleStructure and appearance optimization for controllable shape design.ACM Transactions on Graphics346November 2015, 12
- 5 articlePolyhedral Voronoi diagrams for additive manufacturing.ACM Transactions on Graphics374August 2018, 15
- 6 articleFreely orientable microstructures for designing deformable 3D prints.ACM Transactions on GraphicsDecember 2020
11.2 Publications of the year
International journals
- 7 articleClosed space-filling curves with controlled orientation for 3D printing.Computer Graphics Forum2022
- 8 articleS3-Slicer: A General Slicing Framework for Multi-Axis 3D Printing.ACM Transactions on Graphics416December 2022, 1-15
International peer-reviewed conferences
- 9 inproceedingsTransparent rendering and slicing of integral surfaces using per-primitive interval arithmetic.Eurographics 2022 - Short PapersReims, FranceApril 2022
Conferences without proceedings
- 10 inproceedingsProcedural bridges-and-pillars support generation.Eurographics 2022 - 43rd annual conference of the european association for computer graphicsReims, FranceApril 2022
Doctoral dissertations and habilitation theses
- 11 thesisParametrized growth and procedural noise for mechanical metamaterial design.Université de LorraineMay 2022
- 12 thesisCurved slicing for Additive Manufacturing.Universite de LorraineDecember 2022
- 13 thesisProcedural noises for the design of small-scale structures in Additive Manufacturing.Université de LorraineApril 2022
11.3 Cited publications
- 14 articleFast ray tracing of scale-invariant integral surfaces.Computer Graphics Forum406September 2021, 117-134